The Importance of Mold Tooling in Metal Fabrication
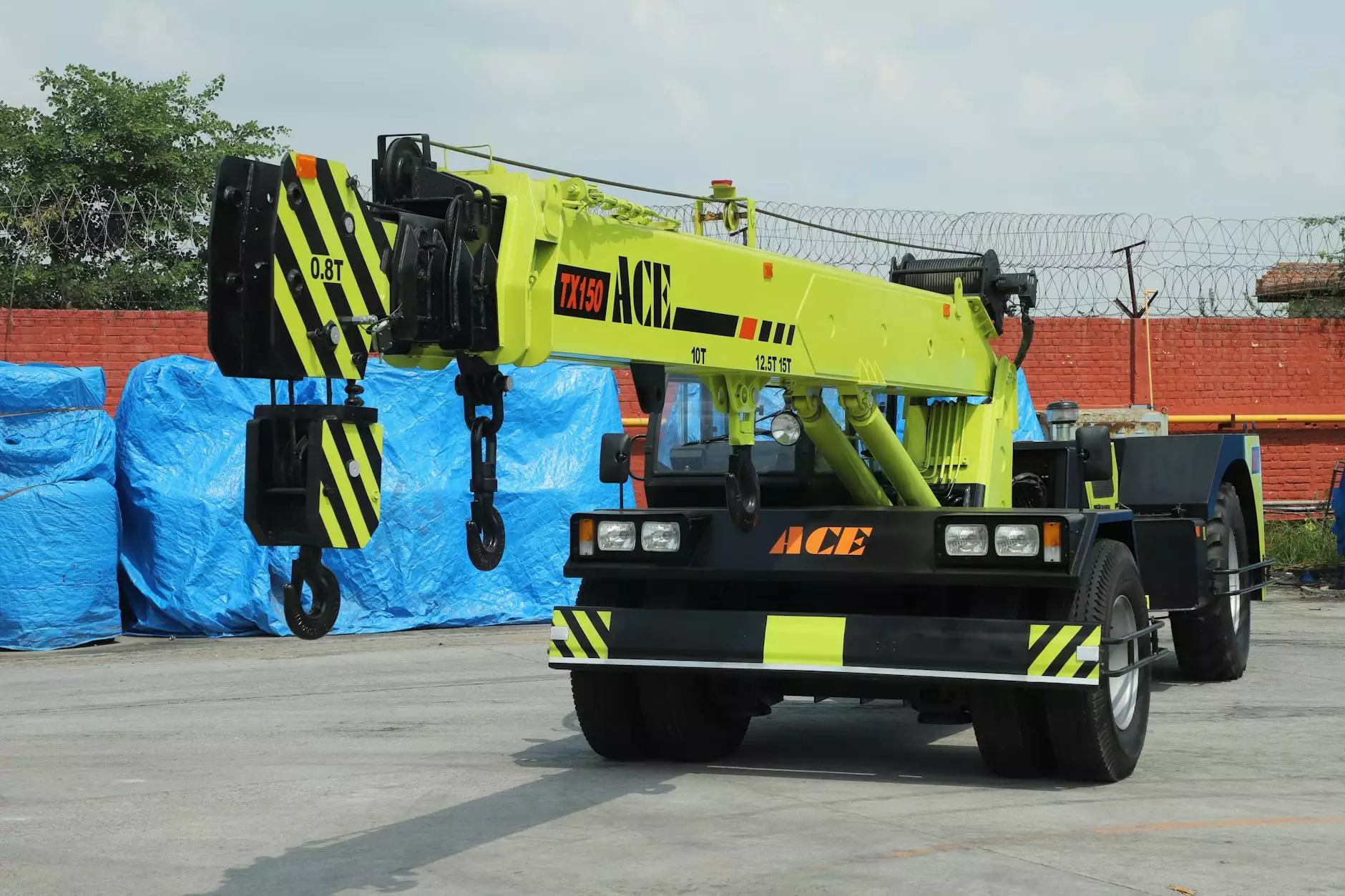
Mold tooling is an essential component in the world of manufacturing, particularly in the field of metal fabrication. It encompasses the creation of tools, dies, and fixtures that are used to shape raw materials into finished products. Understanding the nuances of mold tooling can elevate a business's production efficiency, quality, and profitability. This article delves into the intricacies of mold tooling, covering everything from its fundamental principles to its application in modern metallurgy.
What is Mold Tooling?
Mold tooling refers to the manufacturing processes involved in creating tools used to shape, cast, or form materials, especially metals. The process utilizes various techniques to produce molds that facilitate the mass production of components with precision and repeatability.
Key Components of Mold Tooling
- Molds: The primary component that gives shape to the finished product.
- Tooling Design: The process of engineering molds with precise specifications.
- Machining: The process by which molds are produced from raw materials using cutting tools.
- Maintenance: The regular upkeep necessary to ensure molds are in optimal working condition.
The Importance of Mold Tooling in Metal Fabrication
Mold tooling is of immense importance in metal fabrication for several reasons:
1. Precision and Accuracy
With mold tooling, the production of components can be done with a high degree of precision. This is crucial in industries where tolerances are tight and quality is non-negotiable. Accurate mold tooling ensures that parts fit together seamlessly, promoting efficiency in assembly and improving the final product quality.
2. Cost-Effectiveness
By integrating effective mold tooling processes, businesses can reduce waste and save costs over time. Quality molds lead to fewer defects and the need for rework, significantly impacting the bottom line. Although the initial investment in mold tooling may be high, the savings accrued from efficient production make it worthwhile.
3. Enhanced Production Speed
Custom molds designed specifically for tailored specifications allow for accelerated production times. Automation in the mold manufacturing process can further enhance speed, enabling businesses to meet high demand without sacrificing quality. Faster turnaround times lead to increased customer satisfaction and a competitive edge.
4. Flexibility and Versatility
Mold tooling is incredibly versatile. It allows for the production of a variety of shapes and sizes, making it suitable for numerous industries, including automotive, aerospace, and consumer electronics. This flexibility enables businesses to pivot quickly in response to market demands.
Types of Mold Tooling Processes
Understanding the different types of mold tooling processes can enable businesses to select the most appropriate method for their needs. Here are several primary types:
1. Injection Molding
Injection molding is a process where material is heated until it becomes liquid and then injected into a mold. This technique is widely used in producing plastic and metal parts, integrating efficiency with high quality. It is especially favored for mass production due to its speed and repeatability.
2. Blow Molding
This process is particularly useful for creating hollow parts. A tube of heated plastic is blown into a mold to create the final product. Blow molding is often used in the production of bottles and containers.
3. Compression Molding
Compression molding involves placing a material into an open mold cavity and then applying heat and pressure until the material cures into the desired shape. This method is extensively used for making larger, solid parts and is suitable for various materials, including rubber and thermoset plastics.
4. Extrusion
This molding process involves forcing material through a die to create long shapes with a consistent cross-section. It is frequently used for producing pipes, sheets, and rods.
The Mold Tooling Manufacturing Process
The process of creating molds for tooling encompasses several key stages:
1. Design
The first step involves designing the mold based on the specific requirements of the component. Advanced software tools such as Computer-Aided Design (CAD) are commonly used to ensure the mold meets precise engineering specifications.
2. Material Selection
Choosing the right material for the mold is crucial. Factors such as temperature resistance, wear resistance, and cost all influence material selection. Common materials used include steel, aluminum, and other metal alloys.
3. Machining
This stage involves removing material from a larger block to create the mold shapes. This can include processes such as milling, turning, and electrical discharge machining (EDM) to achieve fine details and smooth finishes.
4. Assembly
After machining, the mold components are assembled. This step demands high levels of precision to ensure that all parts fit together perfectly and function correctly during production.
5. Testing and Quality Control
Before a mold goes into production, it must undergo rigorous testing. This involves running trial productions to ensure that the mold performs as expected. Any necessary adjustments are made during this phase to optimize the mold for manufacturing.
Conclusion
In conclusion, mold tooling plays a pivotal role in the efficiency and quality of metal fabrication processes. Its contributions to precision, cost-effectiveness, enhanced production speed, and versatility cannot be overstated. By investing in high-quality mold tooling, businesses can ensure they remain competitive in an ever-evolving manufacturing landscape. As industries continue to grow and innovate, understanding and implementing effective mold tooling techniques will be critical to achieving success and maintaining high standards of product quality.
About DeepMould.net
DeepMould.net specializes in high-quality mold tooling and metal fabrication services, delivering exceptional results for various industries. With a commitment to innovation and excellence, our expert team is dedicated to supporting your manufacturing needs and helping you achieve your business goals.